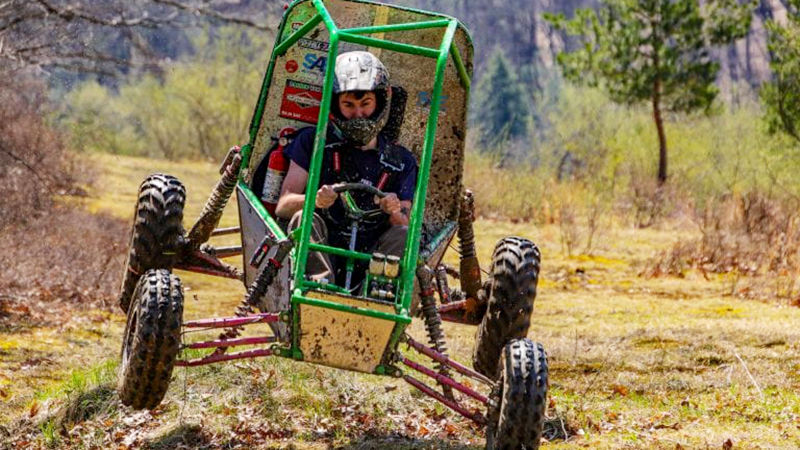
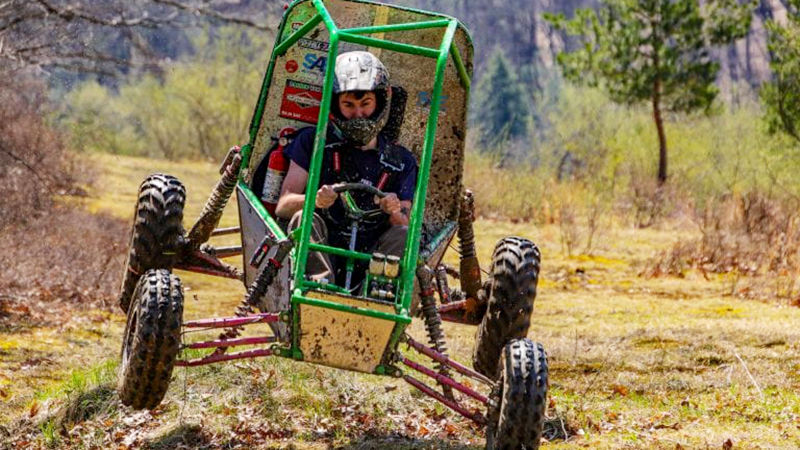
This dialog contains the full navigation menu for this site.
College is not all classes and bookwork. Sometimes it can mean racing around a track in an off-road car you helped build, mud flying, your heart pounding as you bounce inside the harnesses keeping you in place. And yet this, for all the fun it is, is still an opportunity for learning. By the time a member of your club is behind the wheel, your team has already used engineering, physics, production analysis, even sales and communications skills. Penn State Altoona’s Motorsports Club gives students the opportunity to build a Baja race vehicle and race it in the highly competitive Baja SAE® events across the country.
Baja SAE® organizers describe the competition as a simulation of “real-world engineering design projects and their related challenges. Engineering students are tasked to design and build an off-road vehicle that will survive the severe punishment of rough terrain. Each team’s goal is to design and build a single-seat, all-terrain, sporting vehicle whose structure contains the driver. The vehicle is to be a prototype for a reliable, maintainable, ergonomic, and economic production vehicle which serves a recreational user market.”
Sounds simple, right? Design. Build. Compete. To get to that track, though, takes many, many steps involving many, many people with a variety of skill sets. Everything starts with funding. “The students are given a budget by the department,” says Dr. Peter Shull, professor of engineering and former club adviser. “Then they have to drum up additional money. There are also sponsorships by Cummings Motors and some other organizations.”
All teams use the same model of engine, a 10-hp Intek Model 19 engine provided free by Briggs and Stratton. According to Baja SAE®, “Use of the same engine by all the teams creates a more challenging engineering design test.”
Then the hands-on work begins. “The students divide into specific teams,” Shull explains. “One makes the car. One is suspension. One is drive train, frame, etc.” Many of the students working on cars are already familiar with a car engine— “a lot of them are really good at ‘backyard mechanics,’” Shull says. In the process of building the car, however, “you have to train students to shift gears from backyard mechanics toward engineering principles.”
Some jobs require no mechanical expertise at all but still play a critical role in the competition: “They also have a team responsible for design presentation, sales presentation, and someone to take care of budget, and so on, and then people to coordinate with sponsors. This requires significant coordination and leadership.,” Shull adds.
Russ Heaton and Jon Hileman, both Engineering Lab supervisors for machinists and Motorsports Club advisers, work to make sure the students are prepared for the competition. Hileman says, “Our job is to steer them in the right direction and get them ready.” Heaton adds, “They have to pass a stringent inspection system, the frame, the brakes ...” because, as Hileman says, “they have to be spot-on to make sure the car will pass inspection.”
When club members and EMET majors Alex Horwitz, Austin Stivanson, Seth Horwitz, and Ben Leffler are asked about their experience building the car, they all chime in with terms like “CVT,” which means centrifugal variable transmission, and “frame rework,” which means “Seth cut it apart and welded new pieces,” like “Frankenstein,” someone says and everyone laughs. Austin sums it up as “basically we started out with a car we rebuilt from the ground up. And then we took it to competition.”
The 2021 Baja SAE® competition was held at the Drop Forage Testing grounds at the University of Louisville in Kentucky. It’s not just a road race, says club adviser Tom Hatch. “Before the race they have do static (non-racing) tests. The car has to pass a rigorous mechanical and safety inspection. The course is stones and rocks and hill climbs—it’s tough. They go through a lot of different terrain on the track.”
When the students arrived in Louisville in 2021, they found that because of the COVID-19 shutdown a lot of schools had not allowed their students to work on their cars. “We were fortunate,” Austin says. Because the students could prove to Penn State administration that they were all in the same “bubble,” “we were allowed to work in the shop. Other teams were assembling their cars in the parking lots at Louisville. They had all the parts, generators, welders—they worked 24/7. It was crazy.”
Driver: Noah Reighard
Passing inspection isn’t just a matter of kicking tires and looking under a hood (if there was a hood on these cars). “We went through tech[nical] inspection,” Seth says, and it was intense. For example, “we had to bring weld samples. They did an ultrasound to test welded frame joints,” Austin adds. In addition, a representative from Briggs & Stratton shows up for each competition to verify that the engine has not been altered.
Seth says, “We had to pass four different tests: hill climb, acceleration test, braking test, and maneuverability.” Alex did the driving for both braking and maneuverability. Seth drove the S&T (suspension and traction) test, which Alex calls the “rollercoaster thrills event. There are six-foot mounds of dirt to go over and two big drops.” (For those interested in the virtual experience, YouTube is full of S&T videos, some from the driver’s perspective.)
Not everything went smoothly, especially in the four-hour endurance race. “It took us a little to pass brake inspection,” Alex says. “We couldn’t meet the distance.” They ended up, he says, having “to stand on the brake pedal.” But it worked. They realized they had misplaced the pin from the car’s fire extinguisher, which meant it would be considered “unusable. We had to run around to random teams until we found someone gave us one.” Also, the rear axle broke during the race, but the students were matter-of-fact about that. Ben says, “We hung in there a while.” Austin adds, “It’s a four-hour race. A lot of teams dropped out before we did.”
The students stress that, as Alex says, “safety is the number 1 priority.” Seth agrees: “These cars are more safe than street cars.” Drivers are strapped in with a six-point harness and are “handcuffed” so their arm cannot extend past the rollcage. In case of an emergency, though, it is possible to release all the straps at the same time for a quick exit. In the safety inspection the driver completely strapped in has to be able to exit the vehicle in less than five seconds—this takes a lot of practice.
Hatch was very pleased with the outcome in Louisville. He says of the 90 teams to compete Penn State Altoona’s team was “one of five to pass tech inspection on the first try. We were very competitive with other top schools attending the event.”
When the students returned to campus from summer break, Austin says, “First thing we did was unpack the trailer and clean everything up. We had a post-mortem. We all came in thinking the same thing”—“we fixed that broken axle first week of school, grease up to our elbows.” It didn’t take long, “a 30-minute job at most,” says Ben; “we all kind of buckled down.” Alex adds, “We created a new spacer for the axle and fixed the steering rack.”
For one club member, the opportunity to build a car was a big factor in choosing Penn State Altoona. Before Noah Reighard enrolled he took a tour of the campus that included the Force Building, where the Baja car was on full display. His decision was made “when I saw the things they were doing—making their own vehicles.” Now club president, Reighard has “learned to weld, learned how to make custom parts, all of our manufacturing processes, all of our metalworking I’ve learned. I like manufacturing my own custom parts for my vehicles.”
Reighard has found his club experience to have real-life application on many levels. When he graduates, he wants to work in the manufacturing field. “A lot of what I’ve learned here in college is about overcoming obstacles,” he says. During a summer internship in the paper industry Reighard put those lessons to use when confronted with something that needed to be repaired, using a “step-by-step approach, looking for the root cause of the problem.” He calls his club experience “invaluable.”
Not all club members are studying to be engineers. Carollyn Stefanko is a freshman majoring in Asian studies and the secretary of the Motorsports Club. She was attracted to it because “it was different from a lot of other clubs. There’s a lot of hands-on work, actually making stuff. I thought it was so unique.”
Stefanko’s responsibilities are not mechanical. “My main job is the business presentation,” she says. “We create a fake company and do all the logistics behind what a company would do. This year it’s Renegade Motor Sports. We have to create a backstory, fake sales, how many cars we’ve sold and submit a four-page presentation. It’s a lot of good experience but a lot of work, too.”
She continues: “The whole project is really fun. I’m not an engineer and I made good friends and learned a lot of things that are useful. It’s a group of people who are always working together.” New members are taught some of the basics, such as what a suspension is, and how to use tools such as manual mill so Carollyn “got to learn how to use plasma cutters and grinders, things most people would never have access to. I packed bearings with grease.”
Austin Stivanson on the campus test track
The benefits of being a member of this club are undeniable: “Cummings has hired a good number of our EMET students,” Hileman says. In addition, for the non-car-building members: “The whole business plan part is really big. It’s a great resume builder.”
So much is accomplished over the course of the year, with all the focus on building the car and meeting the competition requirements. But then it’s game on! “It was neat to pull in at Louisville and see schools like Purdue and Oklahoma,” Heaton says. And despite the fact that everyone wanted to win, there was a significant amount of sportsmanship. “The camaraderie—it gave me chills. While our car was basically done, other teams were grinding and building. One team we even offered materials to.”
The next competition is in Rochester, New York, in early June and will be the last year for the present car model. In 2023 the competition will require a four-wheel-drive vehicle. Hatch says, “This year provided good experience for the young team, getting us geared up for next year. At the competition we were able to discuss different design ideas with other teams and see what works in a car.”
Looking to Rochester, “the goal is to complete the course,” Austin says. Hatch responds, “I think you guys can do it.”
Good luck to the Penn State Altoona Motorsports Club!