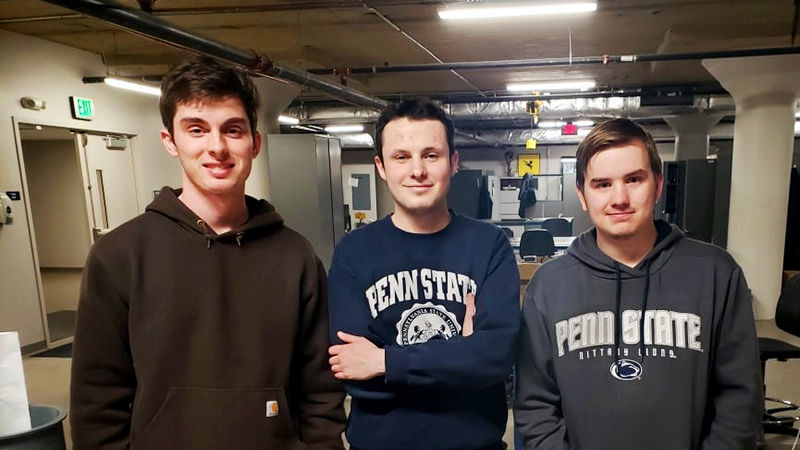
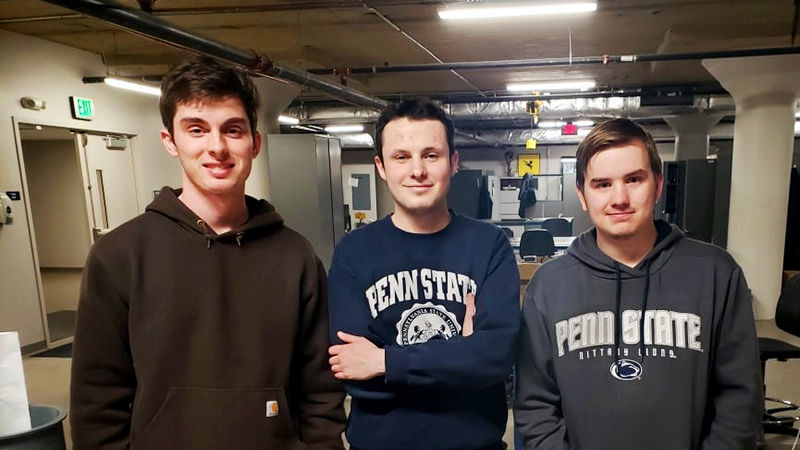
This dialog contains the full navigation menu for this site.
Asphalt roads have been around for centuries, used for foot traffic, horse-drawn carts, and now cars. Their smooth surface—a combination of asphalt, stone, sand, and gravel—makes transportation faster and easier. Over the years, people have developed different mixes to improve durability and performance, but in the end, it is still the same materials, and the result is still a smoother, more resilient road. If it wasn’t for potholes, people might not think about roads at all.
But roads have (literally) hidden potential. Since the 1960s, roads have had inductive loop detectors that trip the red lights based on traffic, but that’s just the tip of the iceberg for what roads can do. One small device—planted in the asphalt—can actually produce energy that will generate electricity. Imagine streetlights that are powered by electricity produced by the cars that drive by. Or the cars themselves being powered in part by that electricity.
The small device needed to generate that power is called a road-compatible piezoelectric energy harvester (RPEH). For their senior capstone project Penn State Altoona electro-mechanical engineering technology (EMET) majors Kyle Fink, Andrew Sherren, and Joshua Eshelman began working under the direction of principal investigators Assistant Teaching Professor of Electrical Engineering Luay Taha and Professor of Engineering Sohail Anwar in the fall of 2021 to develop a prototype RPEH system.
Kyle Fink, Andrew Sherren, and Joshua Eshelman
The system starts with zirconate titanate piezoelectric (PZT) ceramics, known as “stacks,” encased in layers of plastics and steel, which are buried in the road and generate energy when cars run over them. The students’ final report describes the process: “The proposed system first captures mechanical energy using a designed module that transfers the energy to the piezoelectric stacks. Then the captured energy will be converted into electrical energy by the piezoelectric phenomenon. The harvested energy is stored in a storage device, then analyzed by an oscilloscope through the acquisition of the harvested voltage, current, power, and energy.”
The harvester must be able to withstand being run over by vehicles hundreds of times a day and still function, so it needs to be quite durable, making selection of the material used for the housing unit critical. “We purchased an 8ʺ×8ʺ×1ʺ sheet of polycarbonate plastic and used a CNC [computer numerical control] milling machine to create the parts,” Fink says (see diagram). The students then used a 3D printer to create the stack holder using PLA (polylactic acid) plastic.
Consideration was given to using materials other than plastic for these parts. The students consulted with Chris Martin, associate professor of mechanical engineering, who, Fink says, recommended using resin instead of plastic. Martin explains his reasoning: “Epoxy castings can be incredibly strong and watertight. 3D-printed geometries are much easier to fabricate, but they require substantial processing to make them watertight because they are porous by nature. Even if the printing is conducted with 100% fill, ABS plastic is nowhere near as durable.”
In addition, “epoxy casting resins are close cousins of the tough matrix material found in high-end fiberglass and carbon fiber composites,” Martin continues. “With some extra engineering, epoxy resins can be engineered to have a wide range of properties, they sand and cut relatively well, so mechanical processing is always an option to modify the geometry.”
But research projects have constraints: time and money. Martin understands why the students went with the plastic. “I respect the reason the students ultimately used 3D printed materials. The epoxy casting approach requires a mold and a release agent—that means much more fabrication effort. Their project was complicated enough that it was probably worthwhile to triage a little to manage the number of problems they needed to solve at a time. Even if their choice of material is suboptimal, the compromise was a good one.”
The other material critical for this project was the asphalt that the harvester would be placed in. Their report outlines the issues: “It was not feasible to embed our module into a real road due to a multitude of factors: cost, permission, and accessibility to the RPEH for modifications.” Instead, “the RPEH was embedded in ‘Aquaphalt,’ which is a cold compacting asphalt mix used in driveway repairs.”
To simulate a car running over the harvester, the students used a wheel-tracking machine that “applied a force of approximately 700 N to the top of the asphalt at a speed of 26 rpm (1 mph),” which they acknowledge is “very slow”; “the force is much lower than that of a car,” Sherren says. The size of the stacks they used were based on the size of the tracking machine available.
“Our students are working on their bottom layer [of the project’s potential], the actual sensor. They did a great job in harvesting the energy successfully,” Taha says of his students. He sees the RPEH’s potential for more than just powering lights at an intersection. “It’s very important to see how we can make use of this project.” He suggests the possibility of “a wireless communication to all the cars that would give more protection at intersections.” It’s even possible that the harvested energy could be used as a partial powering source for hybrid cars. “It’s a big, big project. I hope that it can be expanded.”
Even now, the project, which was funded by an RDG and Reach Grant Award from Penn State’s College of Engineering, is definitely growing. In addition to Taha and Anwar, three more faculty members work as co-principal investigators: Dr. Shihui Shen, professor of rail transportation engineering at Penn State Altoona; Dr. Hussein Abdeltawab, assistant professor of engineering, electrical and computer engineering technology at Penn State Erie/Behrend College; and Dr. Faeze Ghofrani, assistant teaching professor of rail transportation engineering, Penn State Altoona. Anwar says two more students have been awarded scholarships to work on this project over the summer of 2022. He says, “We are very optimistic about the goals and objectives of this project.” In fact, “we expect to have more joining this project.”
While Fink, Sherren, and Eshelman are now graduated, they still have ideas about future research on the project. Fink acknowledges the next steps could involve hot-mix asphalt and resin as options. “You get a lot better results using a hot mix. That’s the next place to go. You could rerun the tests with resin and compare results,” he says.
Using a real road is envisioned in the future as well. Eshelman was responsible for studying traffic volume. He says, “At some points you have 50,000 [vehicles] and at other points 200,000. You have to target where you’re going to put the module. You want to put them in high-traffic areas because you want the most wattage out of them.”
The option for a “real road” test is coming up. Sherren says that “in the fall they have to design a certain module for the road. They need to do some actual testing on the roads—maybe I-99.”
When asked about their feelings about working on this research project, the students admit that it wasn’t easy. Fink says, “Our biggest problem was getting a grasp on what we were doing—it took all fall. The spring semester it really took off.”
Eshelman says, “It was rewarding. I liked learning the electrical stuff. I learned how a buck-boost converter actually collects the energy.”
“I selected EMET because I had an interest in green energy,” Sherren says. “I jumped at the opportunity to be part of this project.” He appreciates the experience. “We were the first ones doing this project and had the opportunity to lay a lot of groundwork. It was really good to take everything that we’ve learned in college and see how it worked.”