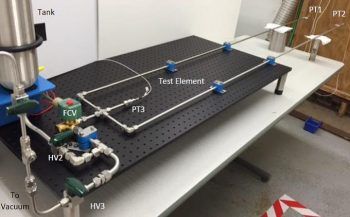
Penn State Altoona faculty and students use this water-hammer test equipment to study propulsion.
ALTOONA, Pa. — Space — so much a part of our lives even though the vast majority of us will never experience it. But we benefit from past exploration every day; just use your cellphone and you are utilizing satellites that came from our efforts in space exploration. To get those satellites into space requires rockets. And to get those rockets into space requires propulsion. We may know how to use propulsion but there are still problems to solve. That’s what keeps Penn State Altoona’s Assistant Professor of Mechanical Engineering Jeffrey Moore interested because, as he said, he’s a “space guy — my passion is rockets and propulsion.”
Moore lays out the basics, which sound simple. “The propulsion system is what maneuvers the satellite," he said. "To get it out into orbit or maneuver it, you need a propulsion system, which houses thrusters and the propellant. Without one your satellite doesn’t move.”
But it’s more complicated than that, of course. “Anytime a satellite is launched into orbit, propellant is introduced to the system before you command your thrusters to fire,” which is known as “priming,” Moore explained. The rate at which the propellant is introduced is critical. “If your system is not built correctly, you can introduce very high pressure transients, which could damage components and fail a very expensive mission.”
At what rate should the propellant be introduced? When does it become dangerous? How can one minimize it? That’s what Moore; Grant Risha, professor of mechanical engineering at Penn State Altoona; Penn State Altoona EMET major (now graduate) Bryce Brindle, ’17; and Joshua Gilbert, ’18, wanted to find out “by studying the peak pressure of the initial impact of the water,” Moore said. “We use water because it’s similar in density and viscosity to hydrazine, the most common rocket propellant used for fuel, which is extremely toxic.” But not water straight out of the tap, he said: “We used distilled water because we don’t want to gum up the valve and lines.”
In order to run the tests, the researchers first had to build the equipment — “a propellant tank, a flow control valve, and a network of tubing,” said Moore. For the test itself, they said they “introduced water into an evacuated manifold, which smacks a dead end, and measured the pressure.”
The water hitting the dead end is called a “water hammer,” or as Brindle said, “a theoretical phenomenon that occurs in closed lines of the tubing from a step change in velocity.” For the experiment, she added, “Water goes out of our valve and pressure transducers read the signal at the end of the line. We wanted to know what would happen. Are these peak events that dangerous?”
Working with water instead of hydrazine didn’t impact the force of the water hammer, but there was a surprise, Brindle said. “The coolest thing about doing research is we didn’t know what sound to expect when we experienced the first bout of water hammer. With the first bang we thought the room was exploding. But at least we were outside the test cell.”
The researchers ran the test numerous times, using different internal diameters, line lengths, and flow control valves, at both atmospheric and sub-atmospheric pressure levels. After the tests were run, the results “were recorded into LabVIEW, which Dr. Risha helped program,” Brindle said, with results varying from “a manifold, a ring manifold, and a straight line.” And, as the group's paper reported, “based upon experimental results, it was determined that the internal diameter, line length, valve flow coefficient, and valve opening response time all contributed to the pressure magnitude of the priming event. It was observed that water hammer pressure levels may be minimized and equally distributed throughout a propulsion system manifold using a ring layout, independent of line geometry, valve flow coefficient, and valve opening response time.”
Their research, titled “Effects of Water Hammer on Propulsion Systems,” was presented at the recent 52nd AIAA/SAE/ASEE Joint Propulsion Conference in Salt Lake City, Utah.
Brindle says he wasn’t expecting to go but while on vacation he received an email from Moore asking him to not only make the trip but also present the paper. “I was super excited. We started working to get this paper finished and then the PowerPoint presentation," he said. He was well prepared by the conference: “They had me studying that PowerPoint like crazy. I presented five times before we left and then one or two times a day.”
Brindle knows the heavy preparation paid off when he attended other presentations. “You could tell who put the time and effort in. Some people didn’t even know what they were talking about because the real presenter couldn’t be there,” he said. He credits Moore with his success, saying “The biggest part is know what you’re presenting. We asked Dr. Moore a lot of questions in research. They may not be important to the total outcome but Dr. Moore was there every step of the way.”
The system research isn’t ending, but in fact is “leading to other experiments,” Moore said. “We are looking at restrictions in the flow lines, near the valves that introduce the flow. In addition, we are examining upstream of the propellant tank to determine the activation time to prime a propulsion system.” He said the final goal of the experiments is that “we eventually want to introduce back to the space community some guidelines for designing safer propulsion systems.”